Cela fait maintenant un bon bout de temps que j’ai conçu et fabriqué de toutes pièces ma scie à ruban, et je n’avais pas trouvé le temps d’en parler. Je comptais initialement tourner une vidéo, mais ma GoPro a cédé avant la fin de la réalisation.
Attention : c’est une machine potentiellement dangereuse et qui doit être manipulée avec précaution. Je n’encourage personne à la reproduire. Aucun plan ne sera fourni ; j’estime que, si vous n’êtes pas capable de la concevoir, vous n’êtes pas à même de l’utiliser sans danger.
Le besoin m’en est venu dès que je me suis mis à la soudure à l’arc : débiter les métaux est toujours compliqué, et la précision souvent moyenne. Il existe de petites scies à ruban portatives qui font ce genre de job, mais elles sont réservées à une utilisation professionnelle.
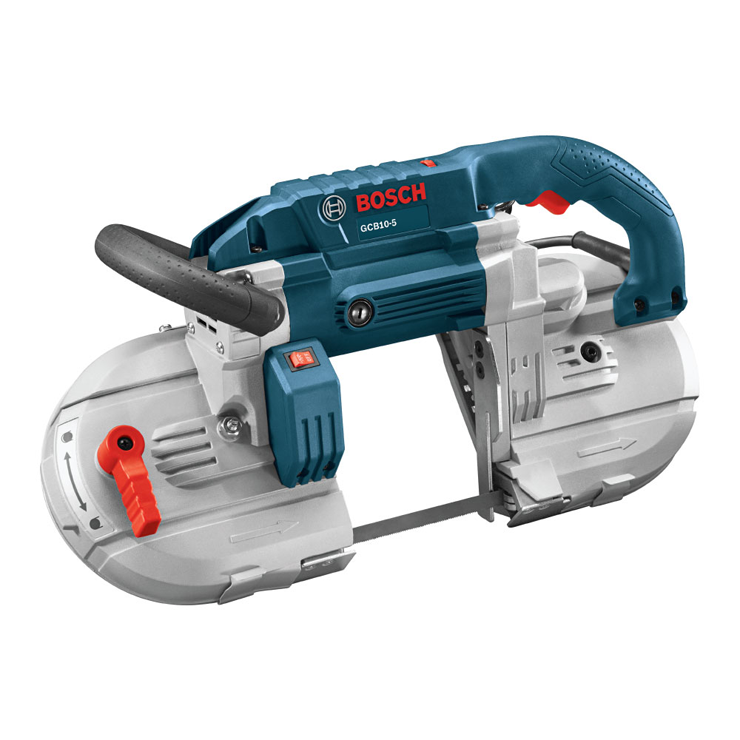
L’idée de la fabrication maison, quant à elle, est surtout due à Matthias Wandel, célèbre youtubeur qui crée lui-même toutes ses machines. Il montre, dans ses vidéos, la réalisation d’une scie à ruban de grande taille conçue pour scier du bois. Je m’en suis inspiré tout au long de ma création ainsi que des multiples techniques qu’il met en œuvre pour obtenir des machines de très bonne qualité.
La première étape a été la conception théorique de la machine sur Sketchup et la commande de la lame directement en Asie : 10 $, pas plus, car cette machine ne doit presque rien coûter.
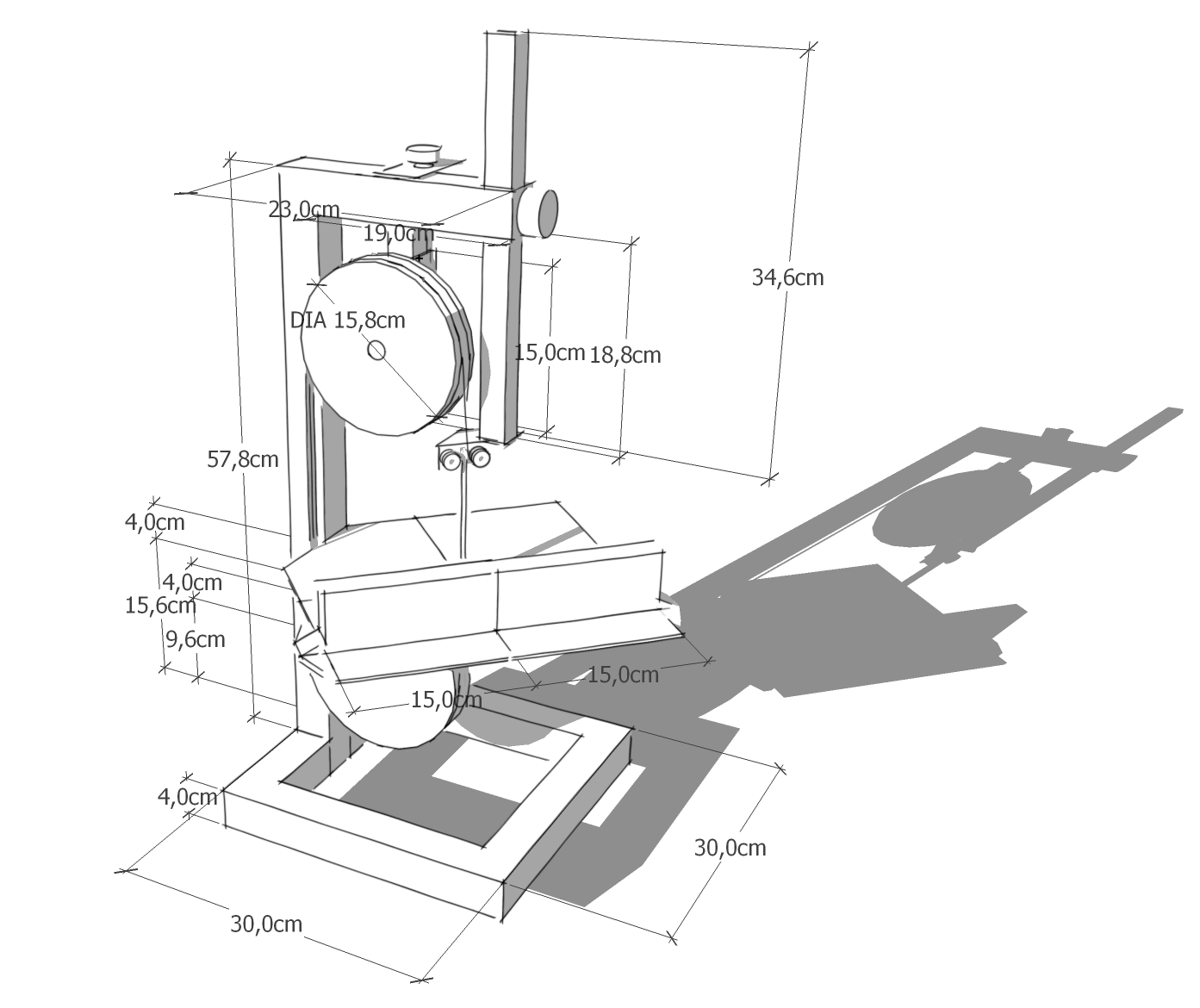
La réalisation se passe sur plusieurs semaines mais demande peu de matériel. Une liste non exhaustive mais rudimentaire :
- Contreplaqué
- Profil carré acier
- Plat acier
- Feuille d’acier
- Vis, écrous, rondelles M8
- Roulements (type skateboard)
- Tiges filetées en tout genre
L’assemblage principal sera la soudure, complétée par de la visserie (impliquant pas mal de taraudage) pour tout ce qui est ajustable : M8 et M5. J’ai commencé par les volants. Initialement débités dans du MDF à la scie sauteuse, ils seront refaits plus tard dans du contreplaqué. La découpe est assez grossière. Ils sont ensuite percés au diamètre 8 et boulonnés sur une tige filetée. De cette façon on peut insérer la tige dans le mandrin d’une perceuse et improviser un tour à bois. Le gros débit est fait au ciseau à bois et la finition au papier de verre. C’est très efficace.
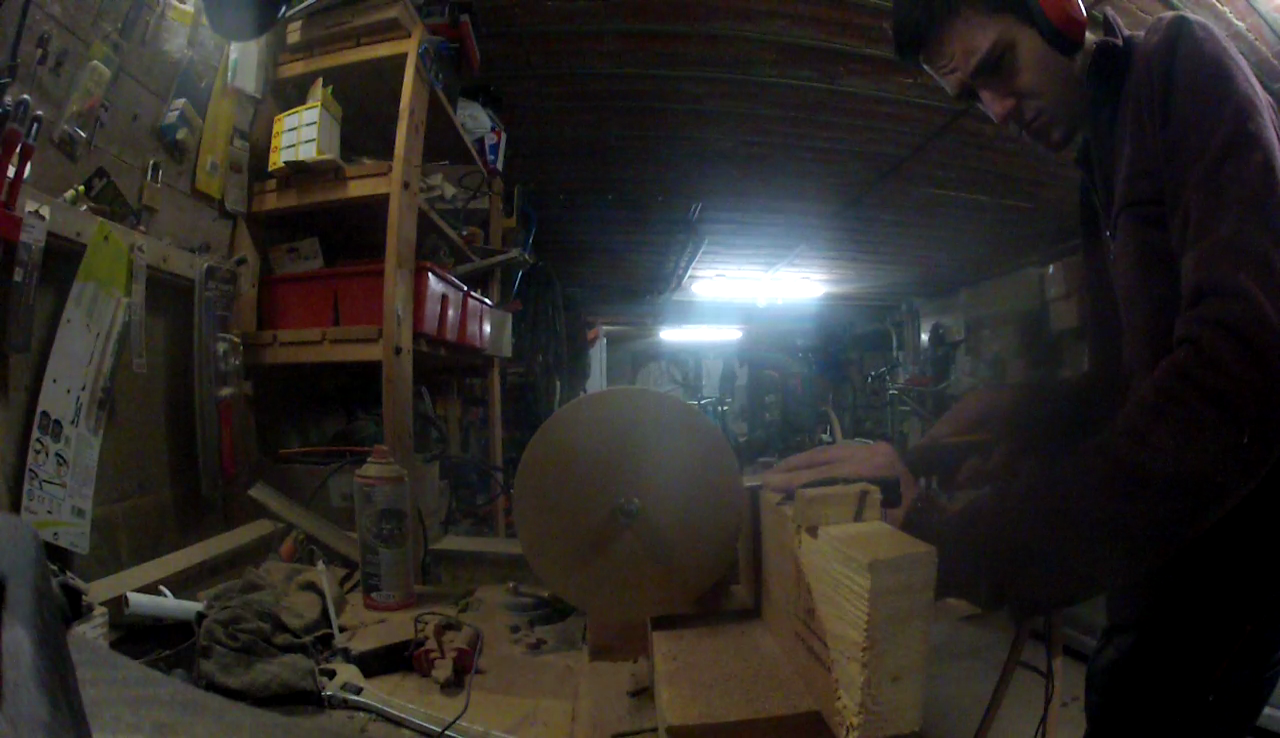
L’idée ici c’est d’avoir deux volants parfaitement identiques et bien équilibrés sur l’axe (tangage) et dont le profil est légèrement convexe ; de cette manière la lame se repositionne au centre du volant tandis que les dents ne sont pas en contact.
J’ai réalisé ensuite la partie horizontale supérieure du cadre. C’est elle qui accueille le guide de lame supérieur et les réglages correspondants. C’est un simple profilé acier, avec un plat soudé en bout, et 5 taraudages pour les réglages.
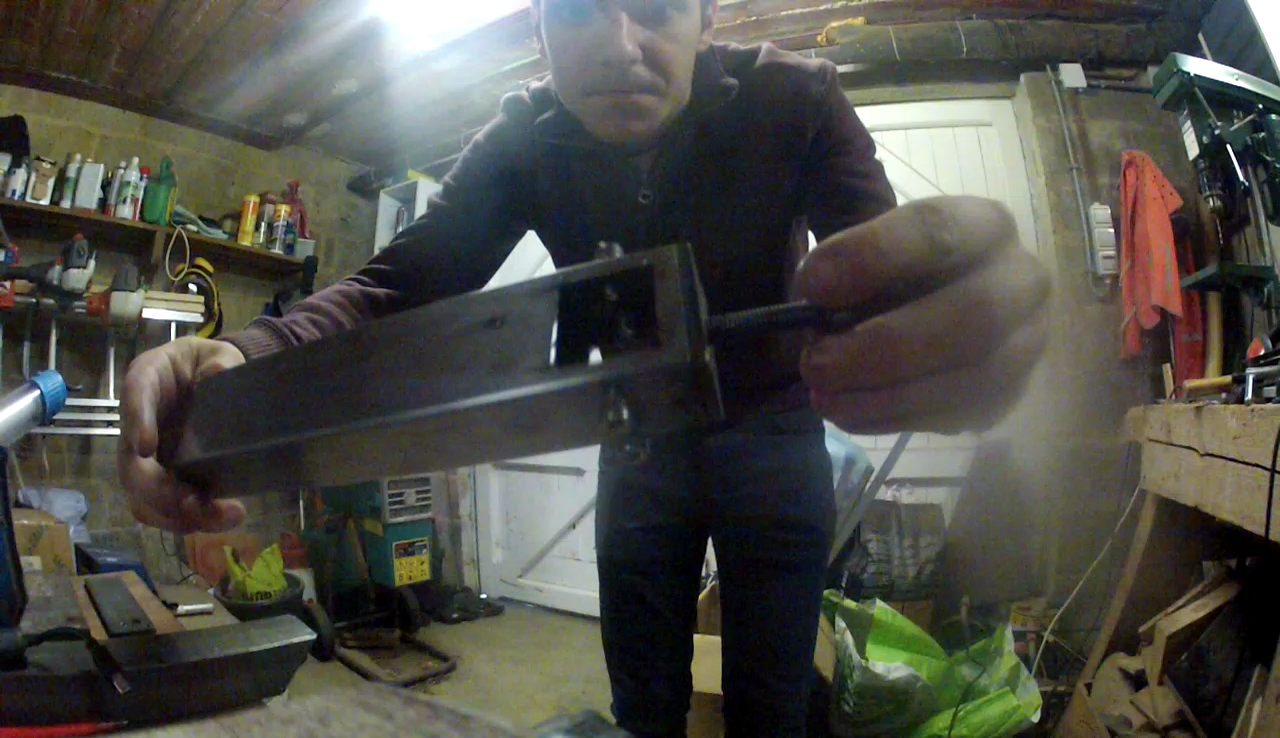
J’ai ensuite soudé tout le cadre. Cette opération m’a donné du fil à retordre… La rétractation de l’acier m’a joué des tours, et les angles n’étaient plus bons une fois les soudures finies. L’avantage ici, c’est que le plan permettait de grandes tolérances, le réglage du volant supérieur étant assez large.
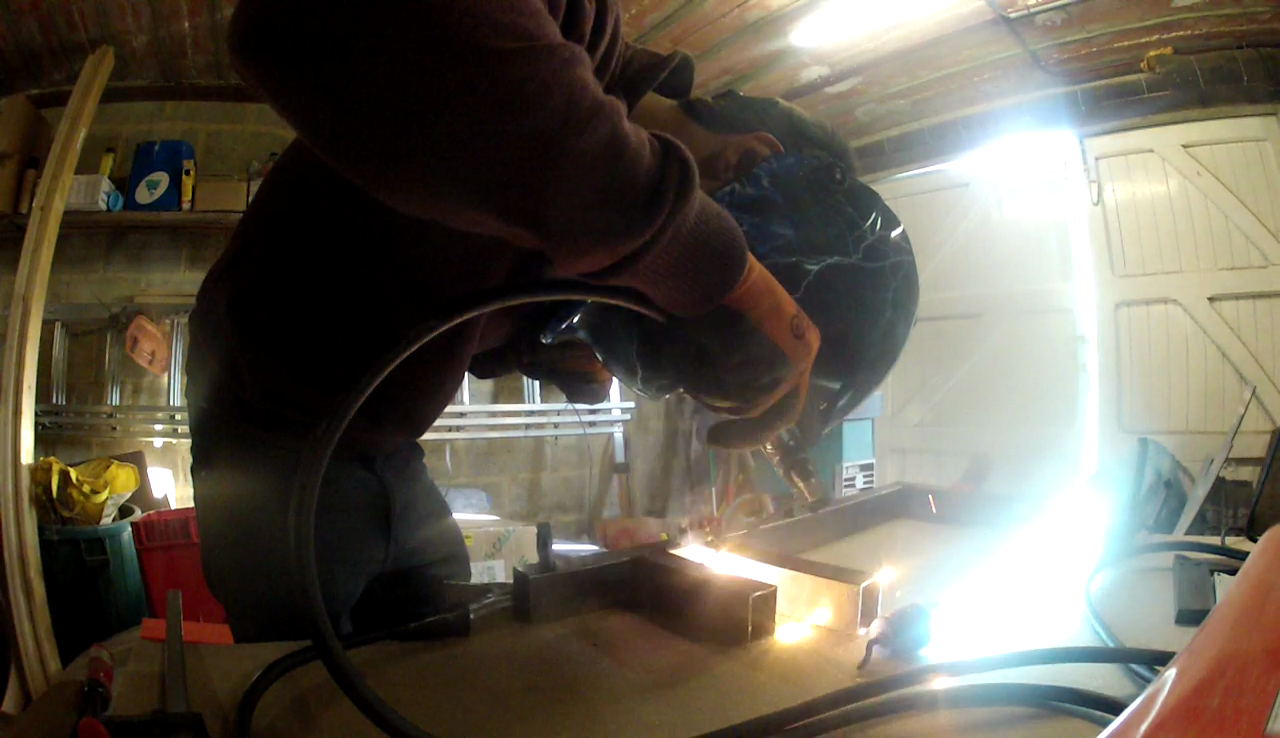
Justement, pour le réglage de la hauteur du volant supérieur, j’ai prévu de faire coulisser une pièce le long d’un profilé carré. J’assemble 6 morceaux de fer plat autour du profilé. L’astuce consiste à pointer les différentes pièces tenues en place autour du profilé. On insère une fine épaisseur (type papier carton) entre les deux pour s’assurer du coulissement.
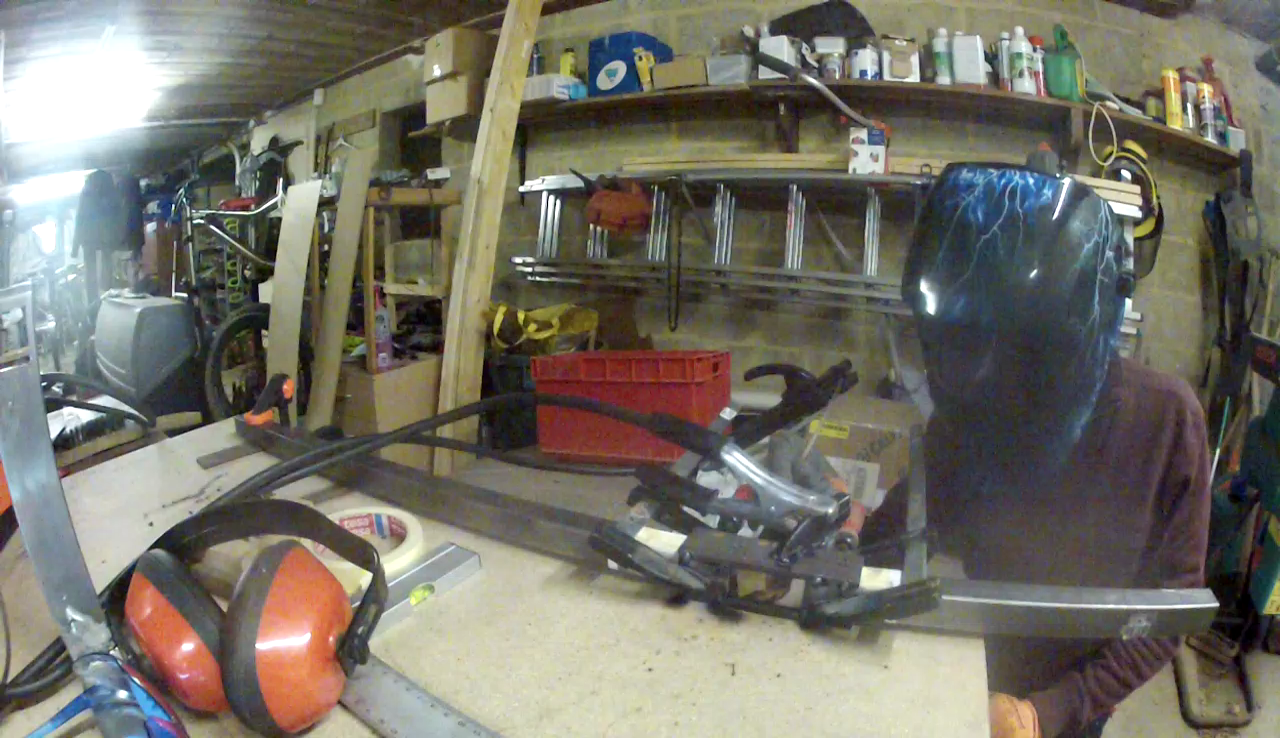
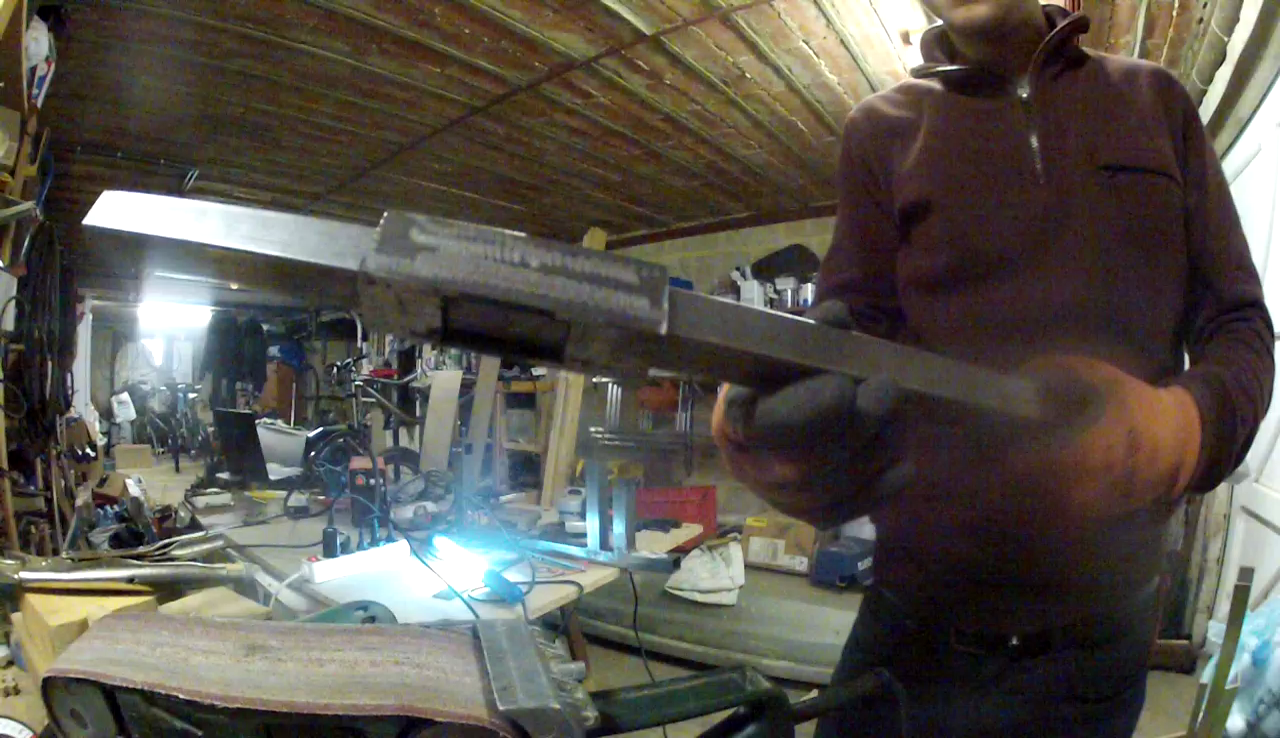
Il suffit alors de débiter une longueur de section carrée et de la souder au cadre pour finaliser celui-ci.
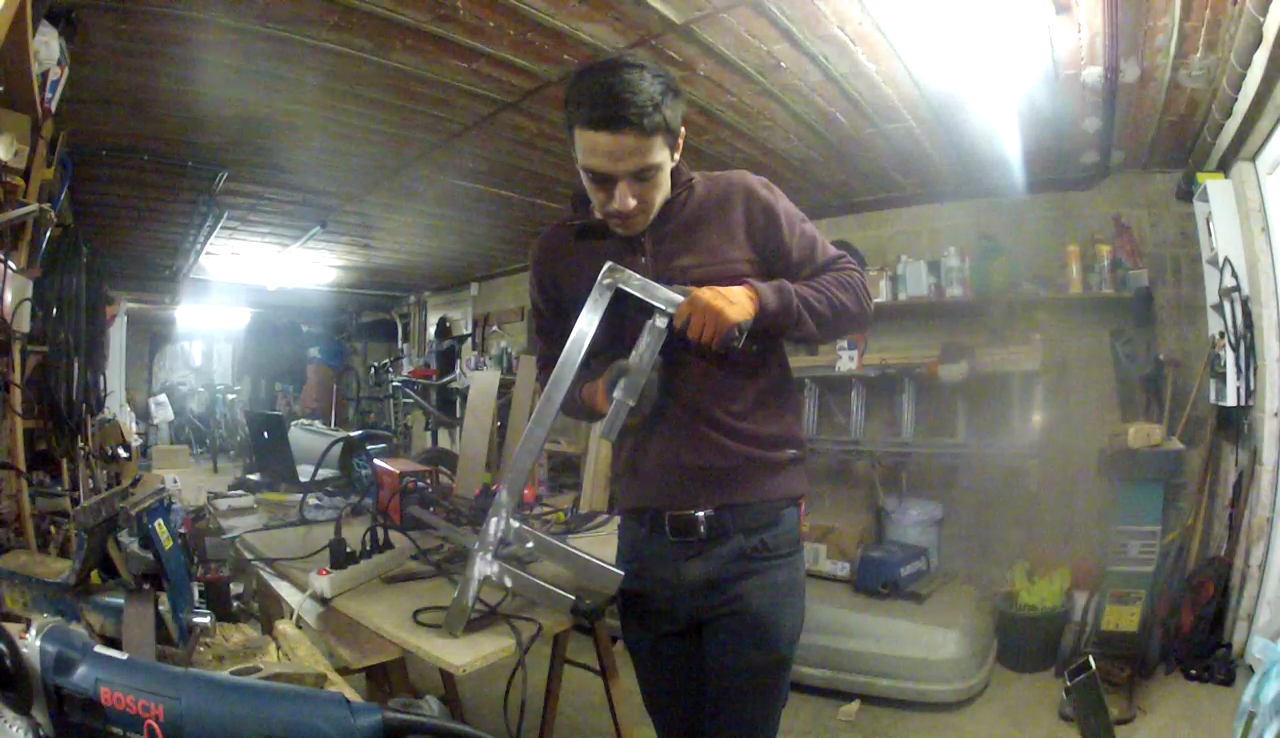
La difficulté ici, c’est que tout doit être dans le même plan : celui des volants. Les soudures ont la fâcheuse tendance de tout faire bouger.
Une tige filetée relie la glissière et le cadre par l’intermédiaire d’écrous soudés. Avec une bonne clef anglaise, on peut faire monter ou descendre la glissière et assurer la tension idéale dans le ruban.
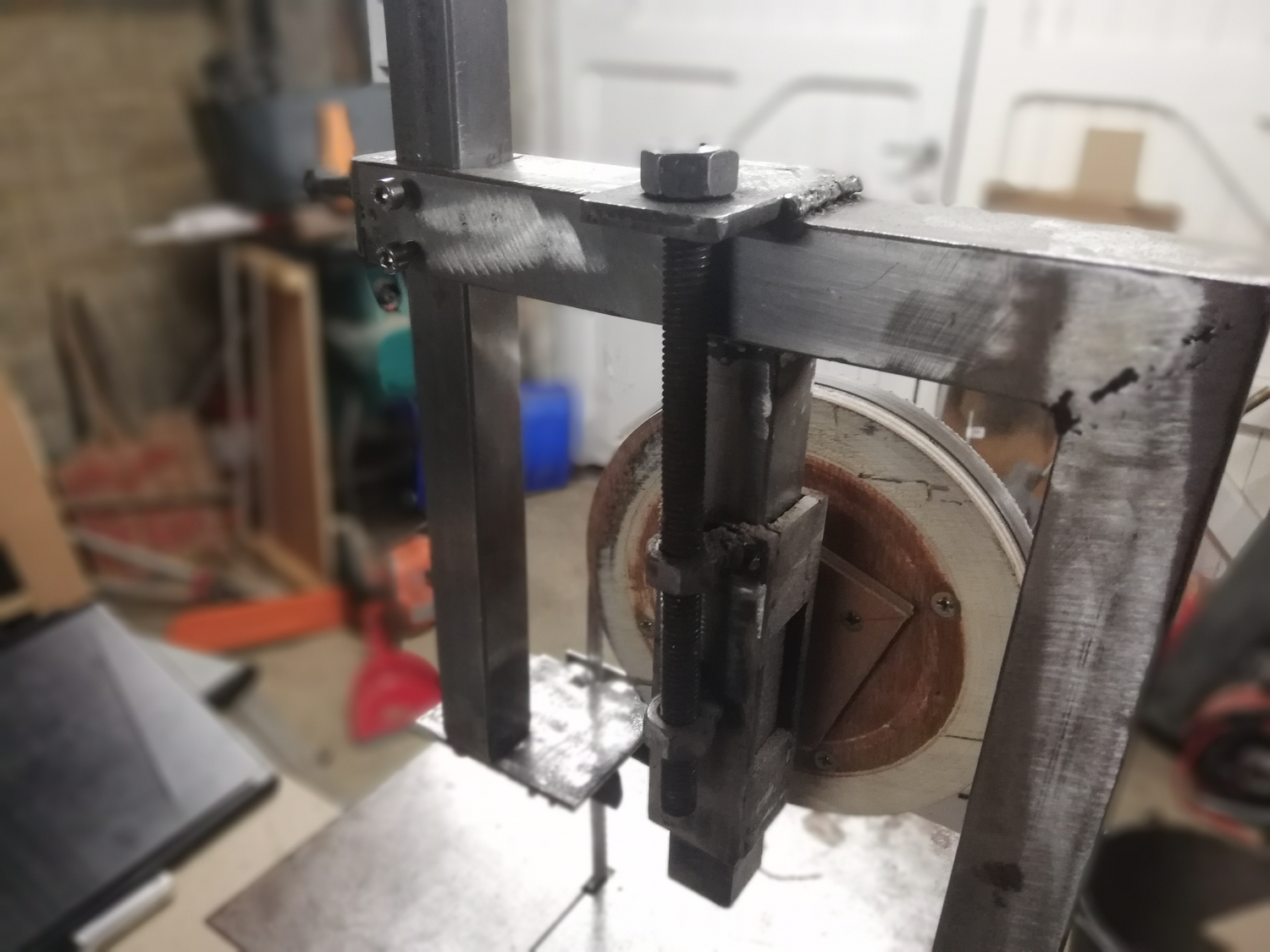
La suite s’est avérée compliquée. Initialement je n’avais prévu de roulement ni pour les volants ni pour l’axe qui traverse le cadre. Non seulement le bruit était infernal, l’usure intense et le filet des tiges filetées s’appuyait sur l’épaisseur du profilé, et en tournant, la tige avançait. Les volants initiaux avaient une rainure dans laquelle venait se loger la lame : après quelques tours, celle-ci l’avait complètement bouffée et s’en échappait. J’avais aussi un sérieux problème d’alignement et de rigidité sur l’axe supérieur.
Je laisse passer un peu de temps pour faire davantage de recherches sur les volants. J’arrive finalement à la solution de modèles à profil convexe en contreplaqué. Ils seront également tournés.
J’utilise des roulements de skateboard de diamètre intérieur 8 mm. Chacun d’eux est logé dans une plaque de contreplaqué. Pour la partie supérieure, j’ai positionné une plaque de part et d’autre du volant, dans un premier temps avec du scotch pour vérifier le tangage. Étape très fastidieuse pour que l’alignement vertical soit parfait pendant la rotation ; le scotch permettait cependant de faire les ajustements nécessaires avant un vissage définitif.
Pour la partie inférieure, le volant est boulonné à l’axe afin d’en être solidaire et de pouvoir être entraîné. Les plaques à roulement sont positionnées de part et d’autre du cadre avec 4 vis dont le pas est taraudé directement dans le cadre. De cette manière, on peut ajuster avec finesse la rotation du volant par rapport au cadre. J’ai passé de longues minutes à régler la rotation des deux volants avec le ruban…
J’ai enfin soudé un pied dans un profilé carré.
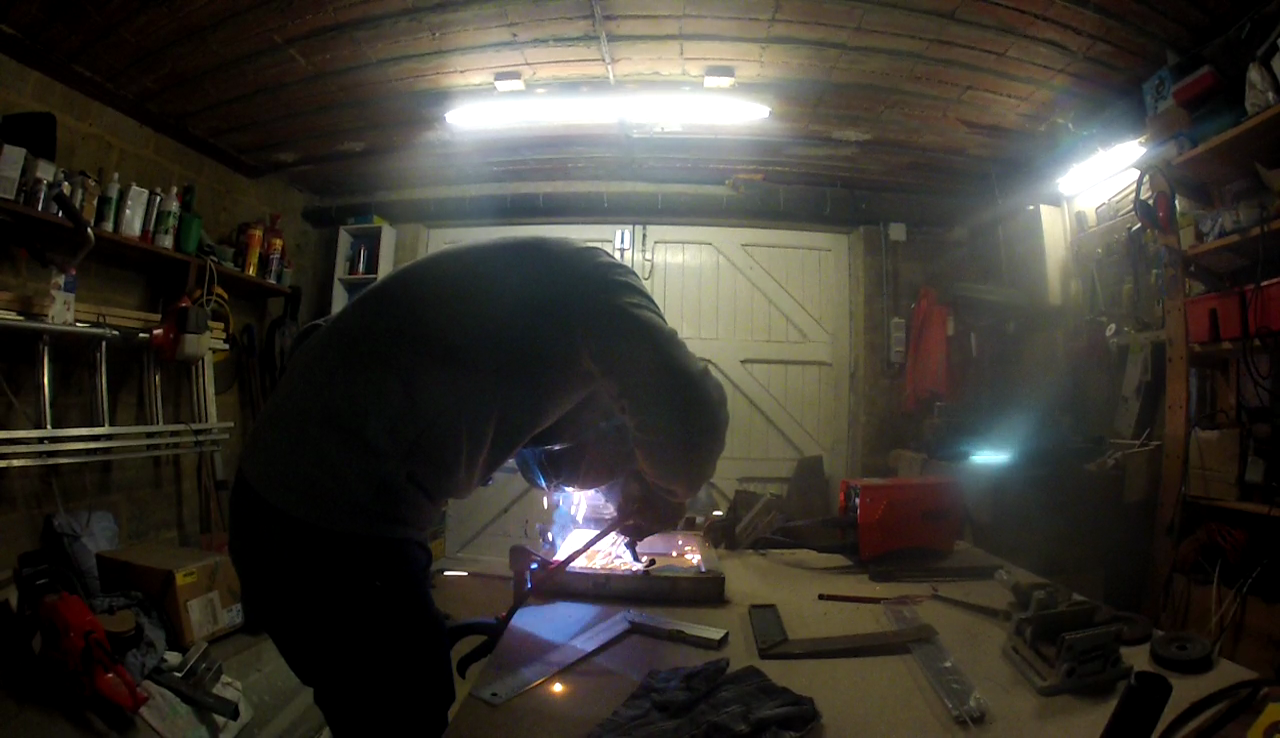
La motorisation se fait avec une ancienne perceuse. Je profite de l’espace existant pour la poignée amovible pour faire un support assez rigide. Il n’y a donc pas de réducteur, la perceuse entraîne directement l’axe du volant inférieur et ça marche assez bien.
Les guides de lame m’ont demandé beaucoup de réflexion et je ne suis toujours pas convaincu de ce que j’ai fait. Quelques constatations :
- Une lame acier est extrêmement rigide et épouse difficilement la forme des volants.
- Plus je tends la lame, plus elle décroche facilement des volants.
- Tordre la lame à 30 ou 45° comme initialement prévu semble impossible.
- La lame ne peut être parfaitement tangente aux deux volants.
En conséquence les guides ont été faits sur place et sur mesure pour cette lame exactement… On est loin du plan imaginé, mais ça reste fonctionnel.
Les guides sont faits de plats en acier soudés. Les roulements de skateboard servent ici de guides pour maintenir la lame en position.
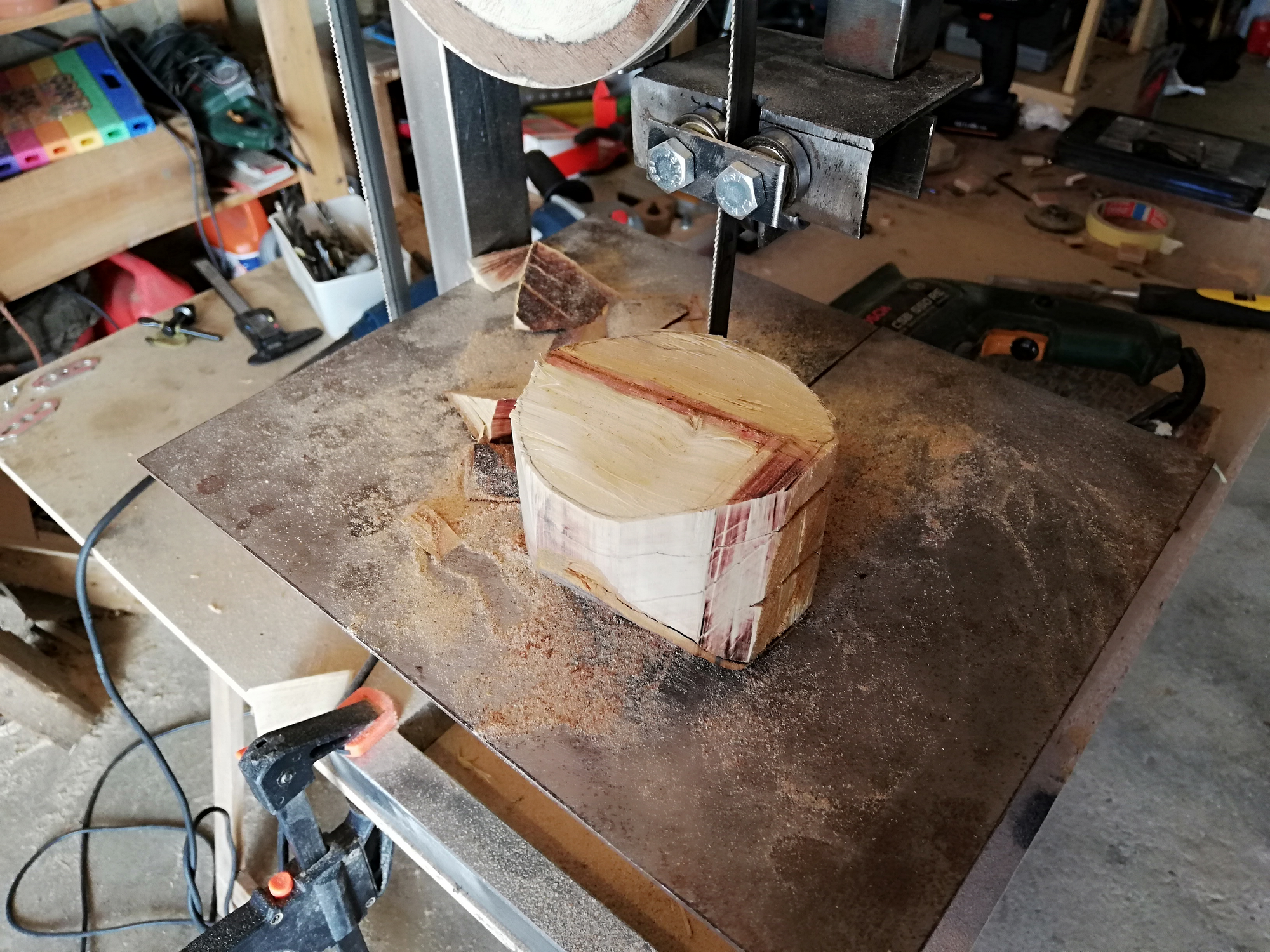
On ne peut voir sur la figure précédente le troisième roulement qui est vertical et sur lequel le dos de la lame vient s’appuyer. On voit qu’un plat vient fermer le guide autour de la lame, l’empêchant ainsi de sauter au visage de l’utilisateur en cas de pépin (ce n’est encore jamais arrivé). Le plateau est une feuille d’acier boulonnée au cadre.
Le résultat : une scie à ruban pas parfaite mais complètement fonctionnelle. Une machine qui ne met pas en confiance, je vous l’accorde, mais qu’on peut finir par apprivoiser.
Quelques conclusions :
- Hauteur de coupe : 12 cm
- Largeur de coupe max : à gauche 15,5 cm, à droite une infinité.
- Profilé acier sans problème, plat d’acier jusqu’à 7 mm d’épaisseur.
- Coût total : pas plus de 50 €.
Je l’ai depuis un certain temps et son côté maison me permet de l’ajuster continuellement. C’est une machine assez fiable mais dont il faut connaître les limites. Malgré ses fortes vibrations, c’est un plaisir de l’utiliser dès qu’on parle d’acier et de précision.
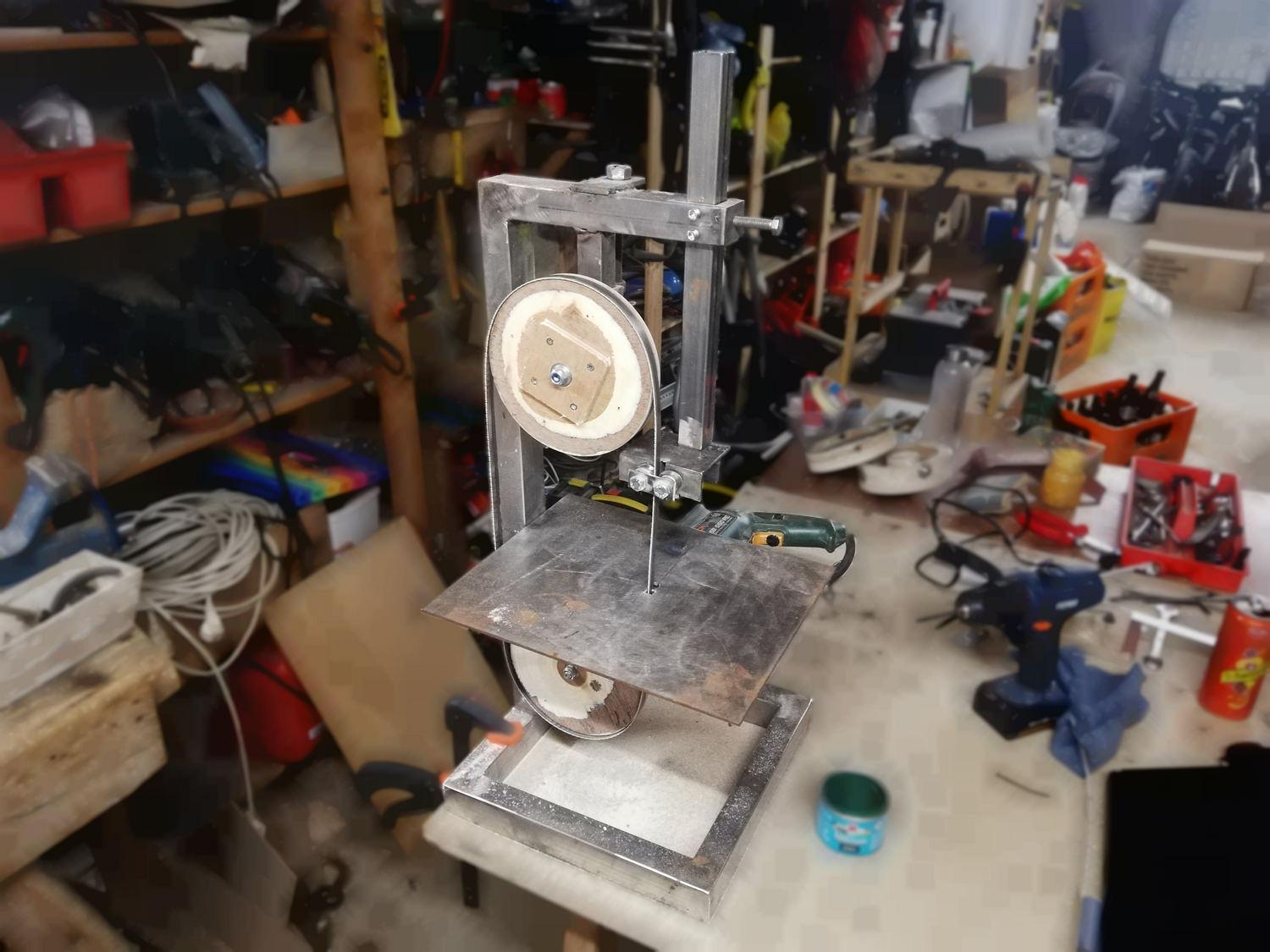
Je compte bien faire évoluer ce modèle en ajoutant un réducteur entre le moteur et le volant inférieur : gagner en couple et en rigidité (axe volant qui peut être plus conséquent). Transformer le montant vertical du cadre en 2 montants formant un angle droit pour ajouter un troisième volant et avoir des rubans bien plus longs : facilement faisable et gain énorme.